exi Project Management were commissioned to provide a multidisciplinary team to design and project manage the construction of a new access stairwell to serve an existing furnace basement for one of our key clients, a multinational metals organisation based in the USA.
Summary
Framework/Partnership // Strategic Partnership
Project Type // Newbuild
As identified from a robust hazard assessment undertaken on the furnace working arrangement; the H&S/operational value of installing a separate stair to an existing furnace basement was identified by exi Project Management. An existing 11m deep basement accommodated 2No NaK VAR furnaces, used to melt 6tonne titanium ingots for the aerospace (fan blade) industry.
As the 2No existing furnace shared a single pedestrian access, the inherent H&S/operational/maintenance risks and constraints were deemed unpalatable for modern manufacturing practices. Providing an additional access route to the basement enabled the two furnaces to be segregated physically unlocking huge operational and H&S benefits to the client as they could run the two furnaces independently from one another, avoid costly outages should one or the other furnace breakdown for any reason and control pedestrian access more effectively. The new stair core enclosure was designed, essentially, to create a 5m x 5m x 8m deep concrete box, with a steel stair assembly within. The project proved challenging in multiple ways:
Firstly, was the deliverance of the project in such a constrained, challenging and ‘service-heavy’ environment. The client has little to no as-builts of the area to inform the design and Preconstruction phase H&S plan. Using some architectural colleagues within exi —we were able to very swiftly develop some CAD drawings to inform and underpin the project. We then sought several critical surveys such as Geotechnical and chemical testing to Ground investigations; subtonic survey drainage CCTV for trade effluent runs adjacent; trial dig holes; asbestos R&D surveys to name a few. This enabled the technical team to develop a suitable design to dig a deep excavation within the factory, adjacent to a live furnace.
Service
The project was extremely demanding, and we were required to navigate numerous significant challenges such as:
- The available working area was physically constrained both in plan and vertically with live services all around. When excavating, we found an area of 4mthick concrete which had to be broken out by a carefully positioned and precisely operated 13tonne pneumatic digger above.
- The surveys and subsequent investigations identified a 11kva electrical cable passing directly through the excavation area at circa 800mm below ground and also an effluent drain within 1m; which we had to respect and protect throughout the duration of the works.
- Due to a high-water table at –2.5m from ground level, we were faced with the difficulties associated with managing water ingress at each stage of the construction. The excavation /temporary works design relied on robust formwork dropping down and additional props and locks adding as excavation got deeper. The concrete used was a waterproof type product and heavy focus was given to the detailing of day joints, reinforcement and workmanship to waterproof detailing. Cofferdams and a pumping strategy were implemented to support construction activities. This was particularly important as significant risk were present with manufacturing processes adjacent as the use of Sodium Potassium (NaK) is a cooling agent s highly volatile when in contact with water.
- Breaking through from the newly formed stair core into the existing furnace wall was critical to avoid unnecessary downtime on the furnace operations. This was coordinated with users to ensure the breakthrough was meticulously planned and works undertaken during the window of opportunity provided (planned maintenance). We were able to successfully break out the 600mm concrete dividing wall and seal the joints between old and new with an appropriate waterproof resin to ensure the joints did not leak.
Given the complexity of the build, exi PM took a Construction Management role throughout the construction phase to ensure all elements were implemented with the utmost care and consideration. The site management team navigated the operational challenges with efficiency, whilst maintaining operations of an adjacent furnace for the duration of the project.
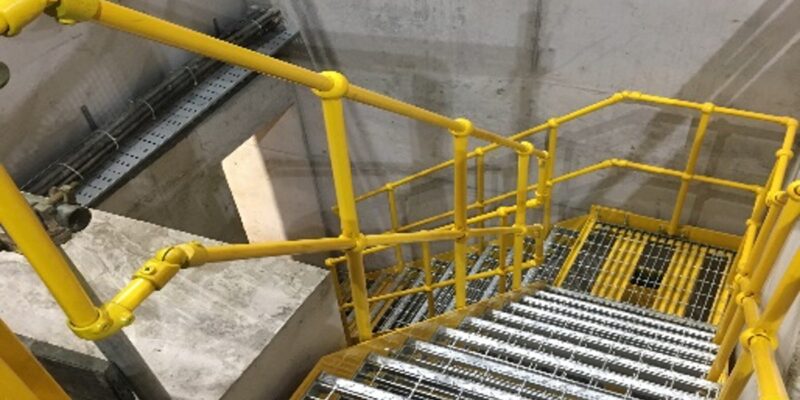
Added Value
Though the project was challenging in many ways, through solid leadership and meticulous planning in collaboration with both the specialist venders and site-based stakeholders, the client’s objectives were fulfilled successfully. This spirit of collaboration, raw determination and resilience are all skills that we are able to transfer to all our projects.
Given the fast paced, results driven culture of the manufacturing environment—we recognise that the clients objectives were focused on timing, programme and certainty of delivery. Our team thrived in the role. Challenges were thrown at us and solutions executed with efficiency – creating and compounding a new base of knowledge in our company for similar future schemes with this client/sector and beyond.
Meeting the LEAN objectives set out in our Project Execution Plan, the new segregated arrangement enabled us to install several SMART technologies to further enhance operation and H&S measures without having to integrate the complex controls systems with the adjacent furnace’s system. Systems such as fortress interlocking systems; laser occupancy sensors, movement sensors for example.
Outcomes
Our successful performance on this project has solidified our longstanding partnership with this client has been rewarded with repeat business and the award of further challenging projects such as the refurbishment of a full furnace a few months later.
exi are proud to maintain our status as the clients “preferred design and construction partner for their UK operations”